Well, “little” in that it weighs 500 pounds and not 1200 pounds like my CNC rig. A little sketching, some layout in Rhino5, then some welding. It’s not finished — it needs side panels and painting — but I’ll deal with that in the Spring after the snow has thawed.
The scale doesn’t show in the photo, but the base is about 32″ off the floor and the top of the drill press is over 6′ high. I’ll be bolting this frame to the floor before any serious use, I’m enough of a safety nerd to not want a 500 drill press toppling over in my shop.

I’ve been using open source software at work since the late 80s and have spent the past couple of years experimenting with Arduino, Reprap, Makerbot, and I’m getting involved with early lasersaur development.
It’s my strong opinion that over the next year open source hardware will really start making an impact in the local and small-scale fabrication space. While there are plenty of shops using EMC2 in large-scale fabrication, the learning curve is steep and EMC2 is focused on subtractive machining operations. There are no fundamental patents on things like mills or lathes to deal with, but a lot of the control circuits and interfaces used are proprietary or at least closed source.
With lasersaur using grbl, Makerbot using (and supporting) ReplicatorG, and the increase of quality tools like Inkscape and OpenSCAD I think we’re finally seeing small-scale manufacturing with a toolchain almost entirely made of open source hardware and software. (I’m not going to wade into the argument about whether or not it’s “real” open source if you’re still buying steppers or power supplies or other COTS items. :-)
In order to help move this process along, I’ve created a new mailing list, opensourcefab, and am working on a wiki/web forum as well.
My goal for this list (and for the forum that will soon go online) is to create a space for those of us who want to use these tools for serious fabrication. Maybe you make/sell model railroad components or build big skeery robots or work at an in-house shop making spares but we’re all interested in the same thing — using open source tools in a production environment.
–jet
My first Instructable, how to make a heated build platform for the Makerbot.
Also, we still have heated build platform kits in the store.
I’ve been really focused on the paying work (which is all NDA), so I haven’t much to post lately.
However, this is kinda cool, my Makerbeam kit finally showed up:
..and I’m already using it to make temporary brackets for stepper motors:
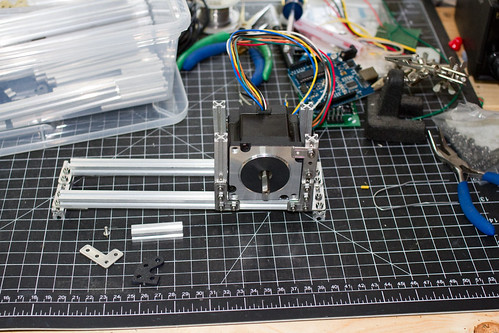
More platforms back in the store and I dropped the price by $10. Now you have an option of a plate with no peripheral holes as well as an option for the nicrhome kit.
Here’s how I set it up: using Kapton tape, I attached a loop of nichrome wire to the underside of the platform. I also put the thermistor in an “average” spot away from the wire:

This connects using the A6 pin on the extruder, same as other boards, all of which are basically doing what Eberhard documented on his blog. For software, you’ll need to download and build the latest ReplicatorG and firmware from the makerbot github.
[tags]makerbot[/tags]
Over the weekend I made myself a couple of aluminum print platforms to experiment with heated print surfaces. I figure that not everyone has easy access to metal-working tools, so I made a few other that I put in my new store.
[tags]makerbot[/tags]
Finally finished my MS Design degree and now have time to write for people other than professors and whatnot. I’ve got a bunch of half-finished posts to clean up, but I’m too busy doing metalworking stuff in the studio to write very much.
The current project is installing a 60G compressor, which also means bolting it to the floor, running hard line and adding a 220V circuit. I hemmed and hawed about which mini compressor to get, then just said “screw it” and went with a big 60G unit. More than enough PSI and CFM for anything I’ll do in my “one-car” sized studio, and when I get real studio space, I’ll move it there.
Still debating what my first air tool should be, however. I’m thinking a die grinder or a sheet-metal nibbler.
[tags]metalwork[/tags]
I’m trying to decide between a Rong Fu RF-45 clone and a Sieg X3. I’m leaning towards a Industrial Hobbies clone, but I thought I’d make up a comparison chart for the Sieg clones for comparison’s sake:
Sieg X3 Clones Comparison Chart in Excel .xls format
Sieg X3 Clones Comparison Chart in CSV
Let me know if you have any corrections/updates.
[tags]metalwork,mill drill,Sieg X3[/tags]
Over on the Yahoo mill_dill group I found an outdated spreadsheet comparing features of the Rong Fu RF-45 square column mill/drill and its various clones.
I’ve been thinking about getting one of these for awhile now for my next art project, so I decided to update the chart. You can find it over on the Yahoo group or download it here:
RF-45 Comparison Chart in Excel .xls format
RF-45 Comparison Chart in CSV
Let me know if you have any corrections/updates.
[tags]metalwork,mill drill,RF-45[/tags]
(Follows is a test of Google Ads.)
After updating the spreadsheet (see the previous entry), I’m thinking the Industrial Hobbies unit is the one I’m after. I can’t afford CNC just yet, but the base machine looks really good.
I’m going to cheap out and try and use it as a general purpose drill press as well. Most of my recent drilling required a bit more accuracy than my Sears drill press was capable of providing. If setup time starts being a problem I can always drop $100 on a cheapo import from HF or Grizzly.
[tags]machining,metalwork[/tags]